Firma Panoval Label S.A. powstała w 1991 roku w Szwajcarii. Bazując na mocnych stronach firmy na Dalekim Wschodzie, w 2017 roku w Ho Chi Minh City w Wietnamie utworzono firmę Panoval (Azja). Ten najnowocześniejszy, specjalnie zbudowany obiekt obejmuje wiele linii powlekania oraz pomieszczenie czyste z certyfikatem ISO klasy 6, w którym można przechowywać wysokiej klasy produkty wymagające najnowocześniejszych technologii powlekania. Firma posiada również certyfikat ISO 14644-2.

Ponad 60% światowego wolumenu etykiet samoprzylepnych produkowanych jest na Dalekim Wschodzie, w tym do zastosowań elektronicznych, medycznych i farmaceutycznych. Jest to główny powód, dla którego firma została założona w Wietnamie, chociaż ogólna własność pozostaje europejska. Pomimo posiadania tylko jednego zakładu produkcyjnego, Panoval współpracuje na arenie międzynarodowej ze sprzedawcami i klientami bezpośrednimi, dzięki czemu zbudował firmę o zasięgu globalnym. Ich elastyczność produkcyjna i reputacja w zakresie elastyczności sprawiły, że stali się wiodącym dostawcą specjalistycznych, niestandardowych materiałów etykietowych. Typowymi klientami są sprzedawcy opakowań elastycznych, przetwórcy etykiet i konwencjonalni drukarze.
Panoval zatrudnia obecnie 25 osób i stale się rozwija. Zespół zarządzający składa się z doświadczonych specjalistów działających na arenie międzynarodowej, z dużym doświadczeniem w opracowywaniu i produkcji laminatów etykietowych do najbardziej wymagających zastosowań. Dyrektor Wilco van Zwieten dołączył do Panoval jako kierownik sprzedaży w 1993 roku i obecnie jest kluczową częścią tego zespołu. Jego zadaniem jest wspieranie nowych przedsiębiorstw, a postęp technologiczny i innowacje postrzega jako kluczowe dla ich sukcesu. Jak wyjaśnia: „Na tak konkurencyjnym rynku to stosunkowo niewielka wielkość firmy i działanie dwóch bardzo różnych linii lakierniczych pozwoliły nam odnieść tak duży sukces. Oprócz większej liczby głównych prac, które wykonujemy, nasz zespół produkcyjny jest w stanie wykonać wiele mniejszych specjalistycznych zleceń, czasami zmieniając produkt trzy lub cztery razy w ciągu zmiany. Do tworzenia kopii zapasowych naszych systemów na bazie gumy używamy najnowocześniejszej technologii klejenia na gorąco UV. Ta technologia UV jako jedyna może potencjalnie zastąpić powłoki rozpuszczalnikowe… nie od razu, ale za dziesięć do piętnastu lat. Aby to zrobić, musisz mieć najwyższej klasy rozwiązanie do utwardzania promieniami UV, ze wszystkimi bajerami i gwizdkami, które wspierają tę technologię. I właśnie to zaprojektowaliśmy we współpracy z producentami maszyn i firmą GEW, abyśmy mogli zaspokoić wszystkie nasze potrzeby w ciągu najbliższych pięciu do dziesięciu lat. Jesteśmy zabezpieczeni na przyszłość.”
Zaprojektowany i wyprodukowany w Wielkiej Brytanii przez firmę GEW, specjalnie zbudowany system utwardzania UV firmy Panoval obejmuje pięć głowic NUVA2, które mogą pomieścić w sumie do siedmiu głowic lamp, zamontowanych na chłodzonym wałku o średnicy 1000 mm na linii powlekania Sung An Machinery (SAM). Lampy są zamontowane wokół bębna na solidnej ramie, która jest oddzielona od zespołu rolek i wysuwana z położenia początkowego na szynach. Umożliwia to dostęp do powierzchni wałka i spodu zespołu głowicy lampy.
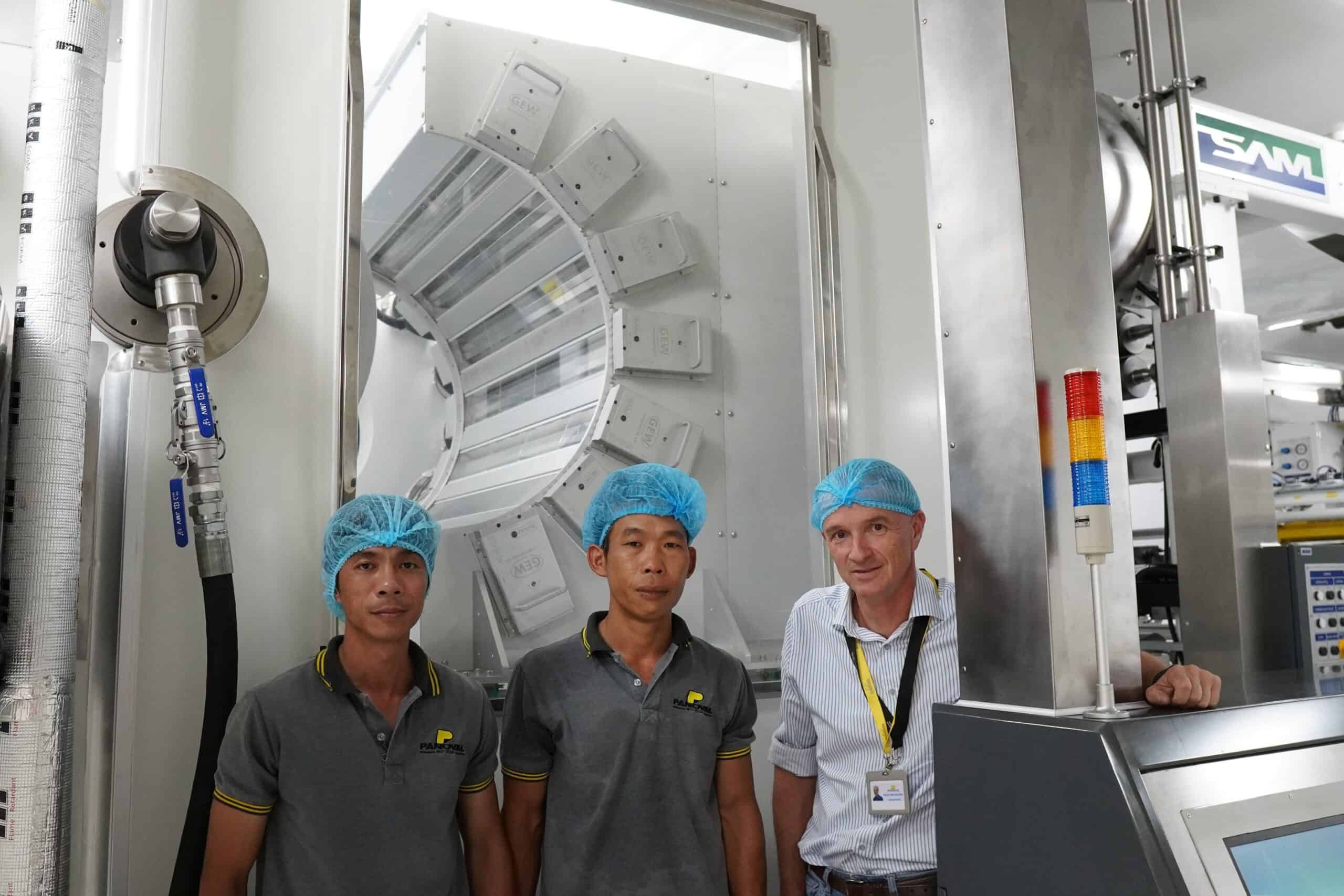
Kiedy początkowo szukał rozwiązania utwardzającego promieniami UV, van Zwieten został skierowany do firmy GEW przez malezyjskiego współpracownika, który niedawno współpracował z GEW przy projektowaniu i instalacji systemu utwardzania promieniami UV do zastosowań w postaci powłok antyadhezyjnych. Van Zwieten wspomina: „Odwiedziłem malezyjską fabrykę, aby na własne oczy zobaczyć instalację, a następnie zacząłem rozmawiać z firmą GEW. Na początku powoli, ponieważ wiedzieliśmy, że potrzebujemy złożonego, zaprojektowanego rozwiązania o wysokim poziomie dostosowania”. Tempo narastało stopniowo, gdy pracował nad wymaganiami Panovala w dziale „Specjalistycznych UV” firmy GEW. Komentuje: „Byliśmy pod wrażeniem ludzi w GEW… ich szybkości reakcji i umiejętności odpowiadania na wszystkie nasze pytania, niezależnie od tego, jak bardzo są one techniczne. Wszystko polega na współpracy z właściwymi ludźmi.”
Następnie Van Zwieten odwiedził zakład produkcyjny GEW w Wielkiej Brytanii podczas budowy systemu, co dało obu stronom możliwość bardziej szczegółowego omówienia systemu i upewnienia się, że jest on na dobrej drodze do spełnienia wszystkich wymagań i oczekiwań. Jeśli chodzi o projekt, instalację i ciągłe wsparcie techniczne dla systemu, van Zwieten nie ma żadnych zastrzeżeń: „Cały proces przebiegł bezproblemowo, nie mieliśmy żadnych problemów. Jeśli pojawi się problem techniczny, dysponujemy zdalnym monitoringiem firmy GEW, który może nam pomóc – ale naprawdę mamy dobre doświadczenia z tym systemem. Kontynuuje: „Do tej pory jedynym zapotrzebowaniem, jakie mieliśmy na usługę zdalnego monitorowania, były automatycznie otrzymywane cotygodniowe raporty, które przedstawiały nam przydatne informacje zarządcze, takie jak czas pracy, godziny pracy lampy, zużycie energii i wydajność. Daje nam to również spokój ducha, ponieważ wiemy, że gdyby pojawił się problem, platforma monitorująca natychmiast go zasygnalizuje.”
Jak podkreśla van Zwieten, przy opracowywaniu specyfikacji nowego systemu utwardzania promieniami UV nie szczędzono żadnych wydatków, aby zapewnić, że będzie on spełniał wszelkie wymagania przez wiele lat. Komentuje: „Typowy laminator zainstaluje jedną lub dwie stacje lamp i będzie zadowolony. Zmieniliśmy się tutaj i zainstalowaliśmy serię pięciu lamp w tandemie, co oznacza, że możemy modyfikować odległość między aplikacją środków chemicznych a utwardzaniem w zależności od zadania, co pozwala nam zaspokoić potrzeby wielu różnych rynków, których obecnie nie można obsłużyć za pomocą tej technologii. Dlatego zdecydowaliśmy się na współpracę z ludźmi z GEW. Mają oni wiedzę techniczną i doświadczenie potrzebne do obsługi tak złożonego systemu. Teraz nie możemy się doczekać szybkiego zwrotu naszej inwestycji, dzięki oszczędnościom energii i nowej pracy, jaką zapewnia nam system UV”.
Rynki docelowe Panoval to przemysł farmaceutyczny i elektroniczny, które wymagają czystszej etykiety o niższych właściwościach odgazowania resztkowego. Van Zwieten wyjaśnia: „Odgazowanie resztkowe ma miejsce wtedy, gdy produkt w dalszym ciągu wydziela gazy po wyprodukowaniu, co może stanowić poważny problem dla producentów. Na przykład w świecie elektroniki odgazowanie może spowodować awarię elektroniki, a jeśli produkujesz drogie elementy, takie jak napędy optyczne, wszelkie czynniki awarii muszą zostać zredukowane do absolutnego minimum, jeśli nie można ich całkowicie wyeliminować. Kontynuuje: „To właśnie tutaj system utwardzania promieniami UV naprawdę nas wyróżnia. Wypróbowaliśmy i przetestowaliśmy nasz proces utwardzania w naszym środowisku produkcyjnym w pomieszczeniu czystym ISO 6 i możemy produkować laminaty o znacznie niższych właściwościach odgazowywania. Dzięki temu możemy zaoferować czystszy i znacznie lepszy produkt tym wyspecjalizowanym producentom i ich przetwórcom.”
Dzięki specjalnie zaprojektowanemu systemowi UV zaprojektowanemu specjalnie dla Panoval można precyzyjnie kontrolować odległość pomiędzy głowicami powlekającymi a lampami utwardzającymi. Oznacza to, że optymalną ekspozycję można osiągnąć w wielu różnych zastosowaniach. Co więcej, system UV został zaprojektowany z siedmioma obudowami głowic lamp i pięcioma kasetami lamp z możliwością zmiany położenia, co oznacza, że głowice lamp można umieszczać w wielu różnych pozycjach, aby skutecznie kontrolować czas świecenia. Wydłużając czas pomiędzy nałożeniem środków chemicznych na podłoże a momentem ich utwardzenia, zapewnia się więcej czasu na ucieczkę niepożądanych gazów przed laminowaniem. Wpływa również na prędkość, z jaką maszyna może pracować; dłuższy okres odgazowania umożliwia skuteczne i bezpieczne utwardzanie przy prędkościach roboczych większych o 50%. Jak mówi van Zwieten: „Dzięki temu mamy ogromną przewagę konkurencyjną nad wieloma firmami amerykańskimi i europejskimi, które ograniczają się do pracy z mniejszą prędkością”.
Demonstrując dążenie firmy do idealnego rozwiązania, firma Panoval zainwestowała również w pięć wielopunktowych czujników monitorowania UV (mUVm) GEW zamontowanych na każdej głowicy lampy UV i połączonych z systemem ERP. Można je mierzyć w środkowym położeniu lampy oraz na skrajnych krawędziach wstęgi o szerokości 500 mm i 1050 mm. Oprócz odczytów miernika cząstek, które dokładnie mierzą poziom odgazowania natychmiast po utwardzeniu, mUVm umożliwia zespołowi produkcyjnemu pomiar i weryfikację, czy w całym cyklu produkcyjnym zastosowano prawidłowy poziom dawki i intensywności promieniowania UV. Dzięki mUVm możliwe jest wygenerowanie certyfikatu utwardzania UV dla każdej partii poprzez rejestrację mocy UV na żywo dla każdej lampy. Dane wyjściowe UV w czasie rzeczywistym są eksportowane za pośrednictwem interfejsu API RESTful.
Jednakże celem van Zwietena jest dalsze rozwijanie zalet systemu monitorowania UV poprzez wykorzystanie jego możliwości raportowania do badania i ustalania optymalnych poziomów energii dla początkowej przyczepności, przyczepności i uwalniania podstawowego asortymentu produktów firmy. Informacje z czujnika UV zostaną następnie wykorzystane do stworzenia trójwymiarowej mapy utwardzania każdej dużej rolki produktu, co zapewni wysoki poziom identyfikowalności dla producentów będących użytkownikami końcowymi. Chociaż dane te są szczególnie istotne dla klientów z branży farmaceutycznej, elektronicznej i lotniczej, można je również wykorzystać do szybkiego i wydajnego konfigurowania powtarzalnych serii produkcyjnych.
Zespół Wilco van Zwietena musiał także pokonać trudności techniczne spowodowane lokalnymi warunkami w Ho Chi Minh City. 18 000 m3/h powietrza wykorzystywanego do chłodzenia jest pobierane do czystego pomieszczenia z zewnątrz budynku o temperaturze otoczenia około 35°C. Zainstalowali dwustopniową filtrację i około 25 metrów dodatkowego przewodu wlotowego, aby obniżyć temperaturę i wilgotność powietrza oraz wszelkie cząsteczki zanieczyszczeń wewnątrz, zanim dotrą one do głowic lamp.
Zespół produkcyjny kieruje się pionierskim sposobem myślenia; skupiają się na wykorzystaniu badań i rozwoju do tworzenia produktów zapewniających użytkownikowi końcowemu przewagę komercyjną. Przykładem tego jest produkcja podłoża do etykiet opon przy użyciu udoskonalonego procesu topienia w promieniach UV. Jak wyjaśnia van Zwieten: „Nie używalibyśmy konwencjonalnego kleju termotopliwego do etykiet opon, ponieważ jest on dość niestabilny, szczególnie przy wyższej gramaturze. Powoduje to, że konwertor musi zmniejszać prędkość przetwarzania, ponieważ ostrza sztancujące szybko ulegają zanieczyszczeniu klejem. Zamiast tego udoskonaliliśmy proces topienia w promieniach UV, dzięki któremu możemy lekko przeutwardzić, aby stworzyć klej o niskiej przyczepności, który ma bardzo wysoką przyczepność końcową. Oznacza to, że konwerter może produkować etykiety znacznie szybciej i czyściej. To sytuacja korzystna dla nas obojga.”
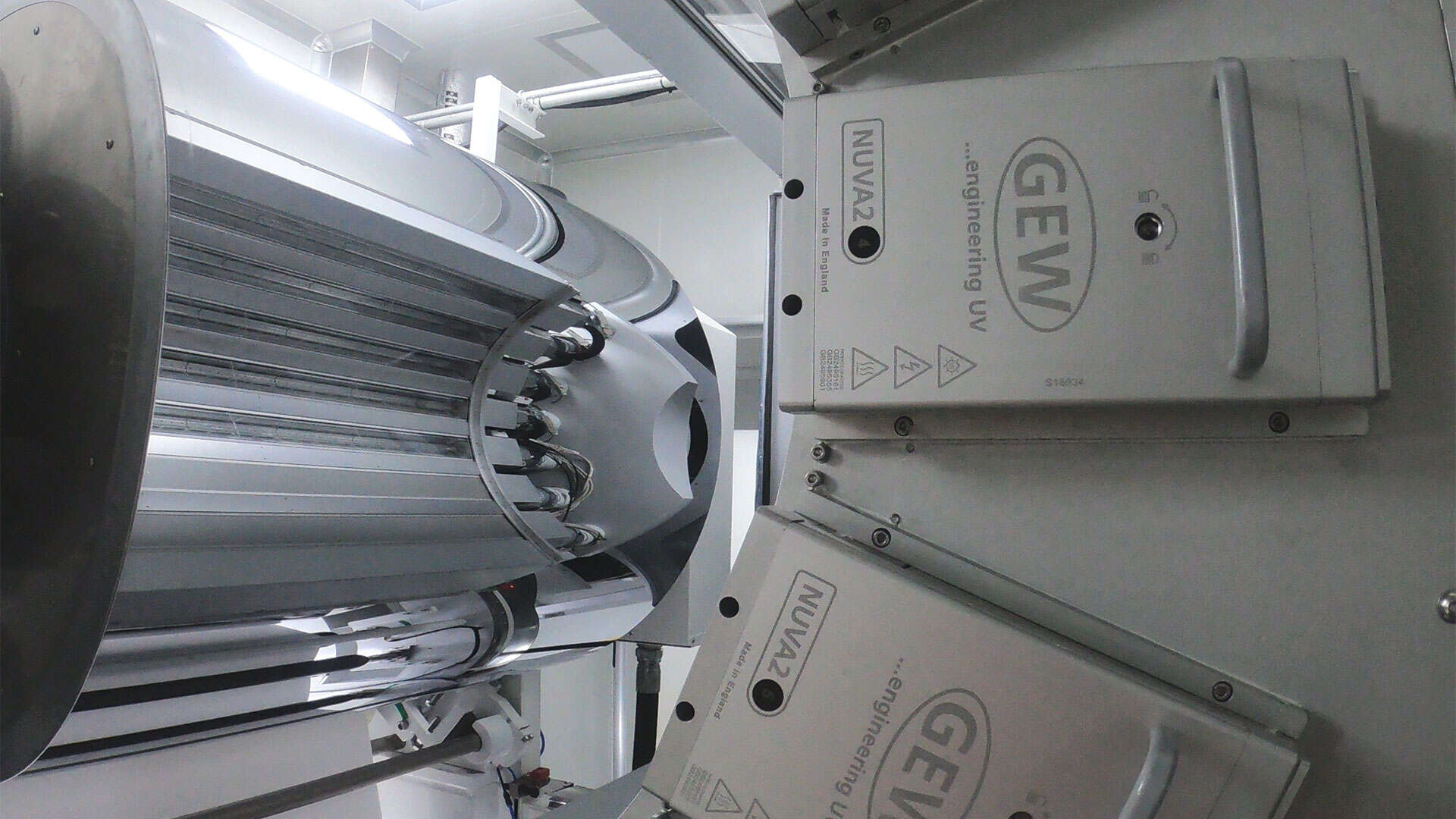
To późniejsze korzyści komercyjne odróżniają ich produkty UV od konwencjonalnych i z nadwyżką rekompensują nieco wyższe koszty surowców opartych na promieniowaniu UV. Co więcej, van Zwieten wskazuje na trend rynkowy, który również działa na ich korzyść: „Coraz więcej producentów powłok produkuje polimery na bazie UV i widzimy, że ceny szybko spadają… w ciągu ostatnich trzech lat spadły już o ponad 40%. To kwestia czasu, zanim promieniowanie UV przejmie kontrolę.
System pięciu lamp firmy Panoval umożliwia zespołowi dostosowanie procesu utwardzania do każdego zadania, w celu uzyskania dowolnego efektu niedostatecznego i nadmiernego utwardzenia. Jak wyjaśnia van Zwieten: „W przypadku niektórych prac konieczne jest podświetlenie i możemy to zrobić, używając po prostu jednej lampy na końcu ścieżki. Zaletą tego jest wydłużenie ścieżki aż o 130 cm, co pozwala na odgazowanie zanim powłoka dotrze do stacji UV. Dzięki temu możemy na przykład produkować etykiety do bardzo wymagających zastosowań medycznych, bez spowalniania naszej linii powlekania”.
Aby określić ilościowo ten wzrost prędkości w kategoriach przewagi konkurencyjnej, van Zwieten kontynuuje: „Możemy wykonywać te konkretne zadania z prędkością do 40 metrów na minutę, co znacznie przekracza normę dla tego typu specjalistycznego produktu. W Europie i USA powszechnie pracują z szybkością 25 metrów na minutę, w wyniku czego są znacznie droższe w porównaniu z podobnymi produktami”.

Etykietowanie do zastosowań medycznych jest często wymagane na podłożach włókninowych, które pochłaniają znacznie więcej promieniowania niż poliestry i polipropyleny. Oznacza to, że regularnie wymagana jest także wysoka moc utwardzania promieniami UV, a nadmierne utwardzanie można łatwo osiągnąć dzięki mocy UV wynoszącej do 108 kW. Utwardzanie promieniami UV służy do naśladowania bardziej pożądanych właściwości klejów na bazie rozpuszczalników, dzięki czemu powłoka jest utwardzana tak, że staje się mało przylepna i sucha w dotyku, ale jednocześnie pozostaje klejem o wysokiej spójności, który wyjątkowo dobrze się starzeje. Proces ten ma inne zalety, jak wyjaśnia van Zwieten: „Przylepność początkowa jest niska i pozwala nawet na zmianę położenia, ale przyczepność końcowa jest bardzo silna – łatwo przekraczająca 50 niutonów – co jest wymagane w przypadku etykietowania o wysokiej wydajności. Następnie wracamy do zalet konwersji, która staje się znacznie szybszym procesem w przypadku powłok utwardzanych promieniowaniem UV.” Podsumowuje: „Możemy osiągnąć wszystkie zalety powłok na bazie rozpuszczalników, ale bez odgazowywania i substancji ekstrahowalnych, które są tak istotne dla przemysłu medycznego, lotniczego i elektronicznego”.
Firma Panoval posiada również okna kwarcowe GEW „HiC” zamontowane w głowicach lamp UV, które szczególnie nadają się do zastosowań w zastosowaniach topionych na gorąco. Ten specjalny gatunek kwarcu pozwala na przedostanie się do powłoki znacznie większej ilości energii UVC w porównaniu z konwencjonalnym kwarcem. Jak komentuje van Zwieten: „Nie poszliśmy na skróty w specyfikacji naszego systemu UV i nie znaleźliśmy jeszcze zadania, którego nie byłby w stanie wykonać. Ponieważ wykonujemy szeroki i zróżnicowany zakres wymagających, krótkotrwałych zleceń, musieliśmy mieć pewność, że zawsze będziemy w stanie osiągnąć to, co chcemy. A jeśli kiedykolwiek okaże się, że potrzebujemy więcej mocy, możemy z łatwością dodać dwie kolejne kasety z głowicami lamp w wolnych obudowach”. Dodaje: „Jednak w obecnym stanie możemy biec na tej linii z prędkością 220 metrów na minutę. Osiągamy dwukrotnie większą prędkość produkcji w porównaniu z równoważną aplikacją na bazie rozpuszczalników. Przykładowo niedawno wyprodukowaliśmy usuwalną etykietę poliestrową z warstwą oddzielającą o niskiej zawartości silikonu, z szybkością 100 metrów na minutę, o niewielkiej gramaturze powłoki i zerowym odgazowaniu… co, o ile mi wiadomo, stanowi nowy rekord świata”.
„System GEW osiągnął dokładnie to, czego oczekiwaliśmy. Nadtwardza, doskonale podtwardza. Oszczędzamy ogromne ilości energii elektrycznej i zmniejszamy nasz ślad węglowy. Jeśli sobie wyobrazić, że nasz stary system wodny wymagał prawie 40 metrów pieców nagrzanych do 200 stopni, aby wydobyć wodę… zużywaliśmy około 1800 kW na godzinę. W przypadku powłok na bazie wody około 40% każdego kilograma stanowi woda, która wymaga ekstrakcji. Teraz dzięki promieniowaniu UV możemy pracować z prędkością 220 metrów na minutę, a maksymalne zużycie wynosi około 600 kW na godzinę. A więc jest trzecia.
Przyjmując procesy utwardzania promieniami UV, należy jednak wziąć pod uwagę inne kwestie, jak zauważa van Zwieten: „Potrzebujesz lepiej wyszkolonego, oddanego personelu do pracy i zrozumienia promieni UV, a także lepszego sprzętu. Dla porównania, w samych Chinach jest ponad 1100 laminatorów rozpuszczalnikowych i są to podstawowe, niedrogie i proste w obsłudze maszyny. Nie potrzebujesz laboratorium. Ale to niebezpieczna gra – jest toksyczna i zanieczyszczająca środowisko, a także kosztuje dużo energii”. Porównując to z zaletami promieniowania UV, podsumowuje: „Dzięki promieniowaniu UV nie potrzebujesz spalarni, nie jest ono toksyczne, nie powoduje ryzyka pożaru, a oszczędności energii i korzyści dla środowiska są imponujące”. Podsumowuje: „Znaleźliśmy w firmie GEW bardzo kompetentnego i elastycznego partnera. Każdemu, kto szuka rozwiązania UV dla kleju termotopliwego, sugeruję do nich zadzwonić.”
Kliknij tutaj, aby uzyskać więcej informacji na temat naszego specjalistycznego procesu UV.